Mexican Talent Drives Digital Transformation at Nissan
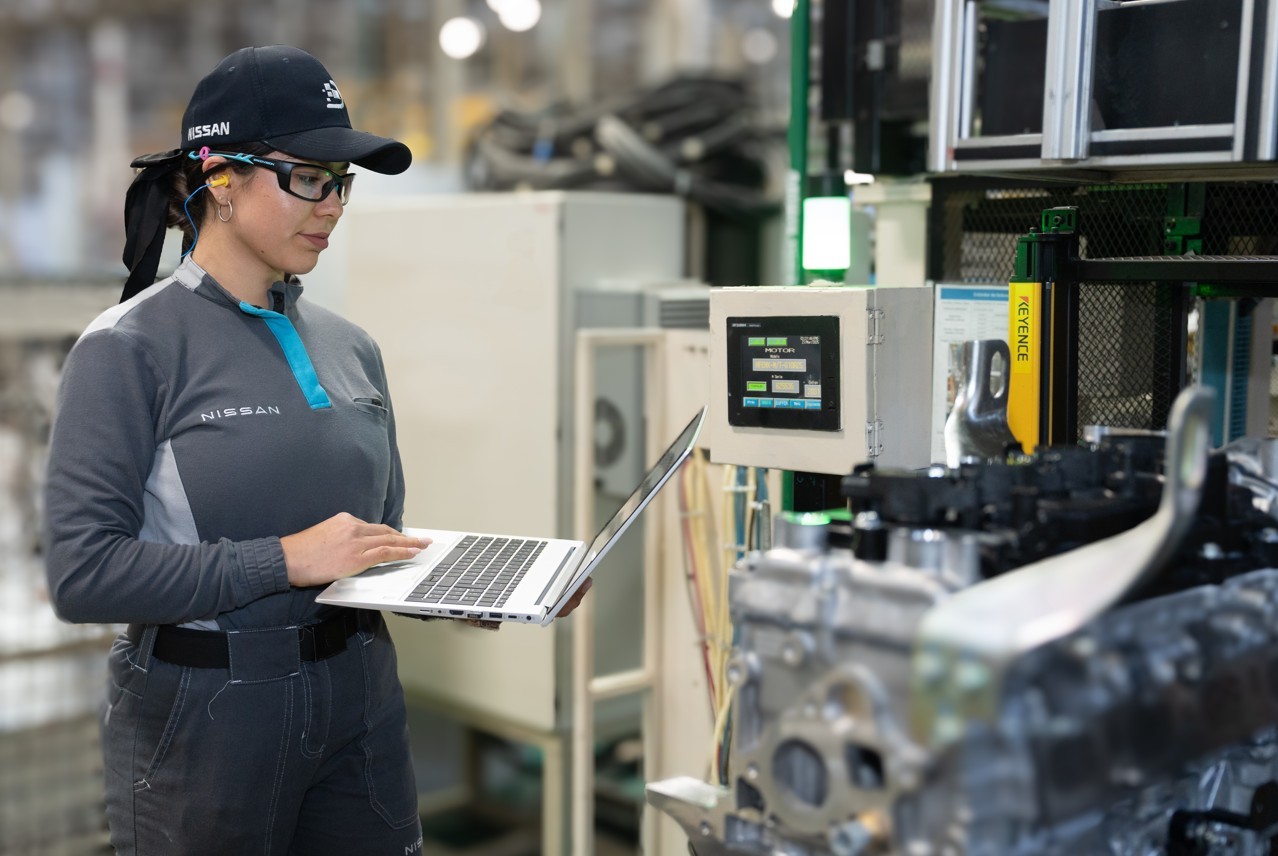
Using its in-house talent as a foundation, Nissan Motor Co. has consolidated a robust ecosystem of digital transformation in manufacturing, integrating advanced automation, real-time monitoring, and predictive intelligence.
In Mexico, this strategic effort has led to multiple improvements in its vehicle and engine plants through the implementation of the Smart E-tools platform, a predictive system developed by its own employees that converts torque data collected on the assembly lines into automated decisions for the preventive maintenance of critical tools.
Since its implementation in January 2025 at the engine plant, this set of processes has had a concrete impact on operations: it has reduced corrective failures by 3% thanks to proactive monitoring of key metrics such as CP and CPK, process capability indicators that measure the consistency and stability of torque values against quality standards.
In addition, it saved up to 4 hours per week in administrative tasks by automating maintenance planning.
Smart E-tools was developed by Jocelyn Guevara, Production Control Systems Specialist; Santiago García, Engine Assembly Maintenance Specialist; and Guadalupe Barajas, Senior Project Engineering Specialist.
“With complete traceability of each tool's usage history, Smart E-tools enables detailed pattern analysis, allowing for proactive adjustments and greater precision in resource management. It has also contributed to a 20% improvement in process stability by detecting and correcting deviations before they affect product quality,” Guevara proudly comments.
In addition to the aforementioned platform, Nissan has implemented two other comprehensive solutions in the region that align with this vision of smart production, enhancing operational efficiency, traceability, proactive maintenance, and talent empowerment.
Smart Management: This is a real-time visualization system through Control Rooms that allows plant supervisors to make immediate decisions based on live process and production data. It also facilitates remote interaction with experts through collaborative video.
This contributes to improvements in the quality and efficiency of its plants, achieving record productivity (units per hour) by reducing average repair times, standardizing technical processes, including augmented reality training through digitized operation sheets, and greater autonomy for field teams, agility in fault diagnosis, and greater operational reliability.
Automation and smart connectivity: Initiative that includes the implementation of servers, networks, and infrastructure.
In Mexico's operations, connectivity increased from 60% in April 2023 to 79% in April 2024, enabling the implementation of process efficiency improvement projects, with visible results in projects such as the new Nissan Kicks.
Digital Training
This consolidation of the digital manufacturing ecosystem is the result of training more than 20 manufacturing leaders in power skills (key capabilities) such as adaptive leadership, strategic thinking, and Design Thinking in partnership with the Massachusetts Institute of Technology (MIT).
Partnerships have also been implemented through an agreement with the Institute of Science and Technology of the State of Aguascalientes (INCyTEA) in Mexico, through which 30 Nissan employees received scholarships in automation 4.0, taught by doctors in information and communications technologies.
It was precisely within the framework of this partnership that Nissan employees came up with the project called Smart E-tools.